Last year, we stripped and repainted the blue “library”. This summer, Kathy decided that her home improvement project during the break would be to strip the lead paint from the “office”.
I moved my work setup into the blue room and she worked on stripping the paint and then the whole paint prep started again. I’m not going to go over all the details since it’s basically the same as the previous room.
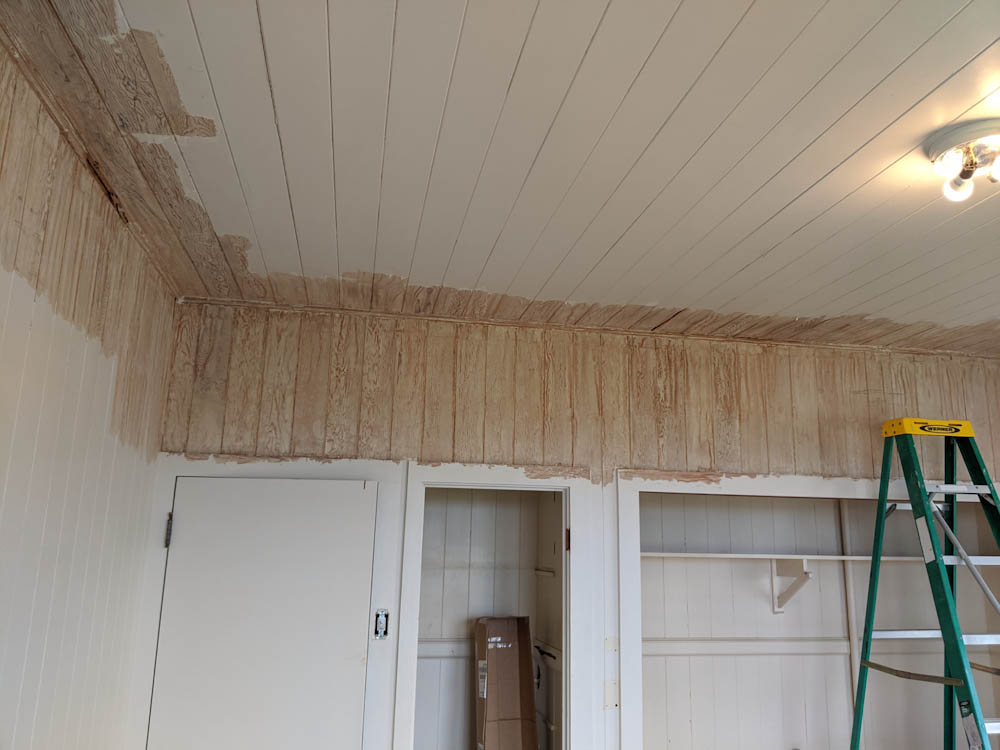
Kathy started by stripping the intersection between the walls and ceiling. This is tricky because of the moulding. Some of it was also severely termite damaged as is visible on the left.
Termite damage was more severe in the walls in this room, especially the closets, and there were some planks in the ceiling that were completely eaten through. We filled most of that damage with Bondo, which is handy because it’s liquid enough that you can get it into the termite galleries.
The house paint scheme that Kathy made up when we started repainting specified a warmer tone in this room since it’s on the north side of the house and only gets direct sunlight immediately after sunrise and before sunset during the summer months. A room with only indirect light will look a lot cooler unless the room is painted in a warmer tone that compensates, so this room was painted in “Grand Sherbert”, a color somewhere between orange and salmon.
We also replaced the old ceiling light fixture in the center of the room with four 1’x1′ 11W flat LED panels. We already use these in the kitchen and really like them. At full brightness, they provide plenty of light, but they’re also dimmable down to a very low level. They even have a switchable color temperature.
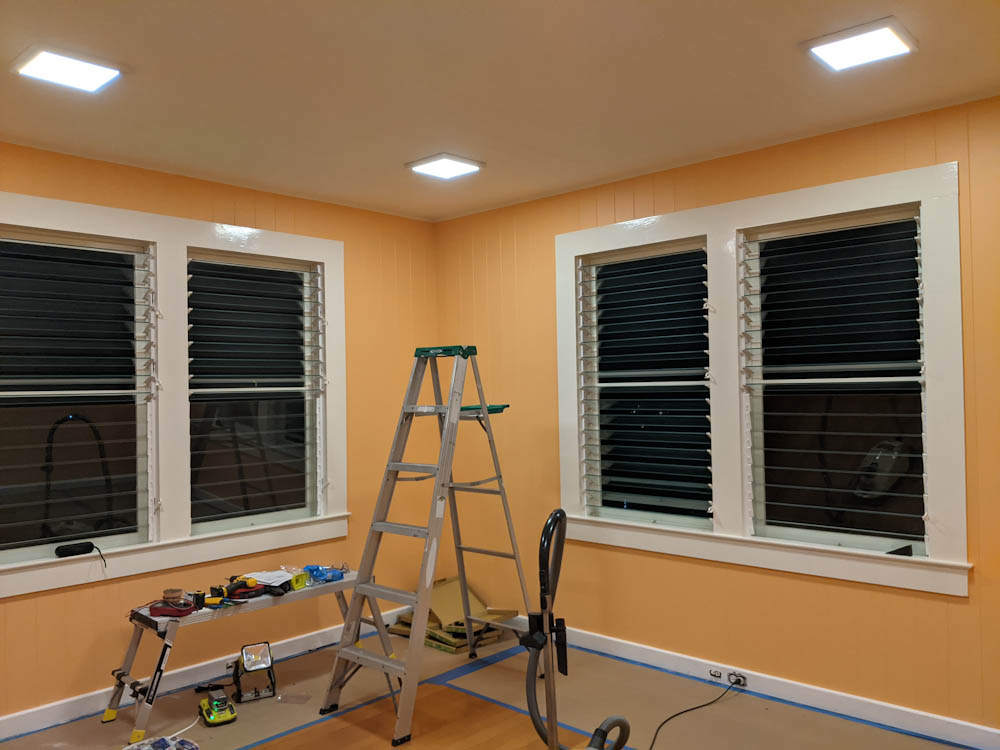
Walls are done, and we’ve also replaced the ceiling lights with four flat LED panels. Note how different the wall color looks in this picture compared to the one above.
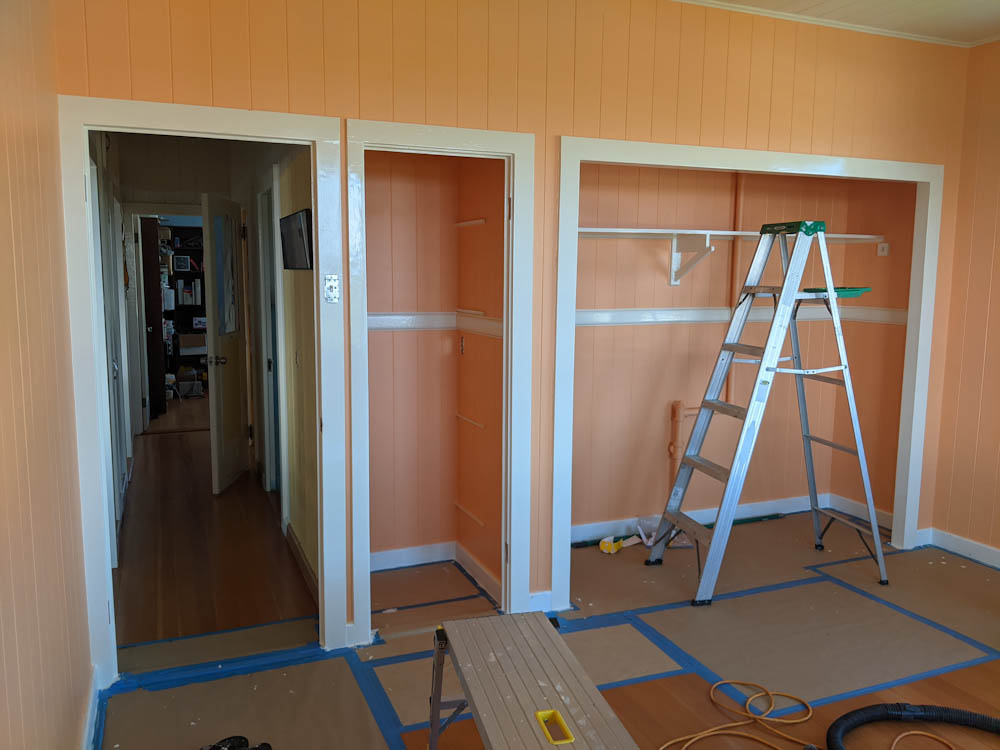
The last thing, as usual, was to put the Eco Brilliant on the trim. (The baseboard will be painted after the floor is redone.)
Since we already had all the furniture out of the room, we also decided to touch up the floor finish, which has received some scuffing over the 7 years since we refinished the floors. , especially where my office chair had pressed the rug into it. The oscillating sander made a brief reappearance to abrade the old finish and then I added two coats of Bona Traffic HD.
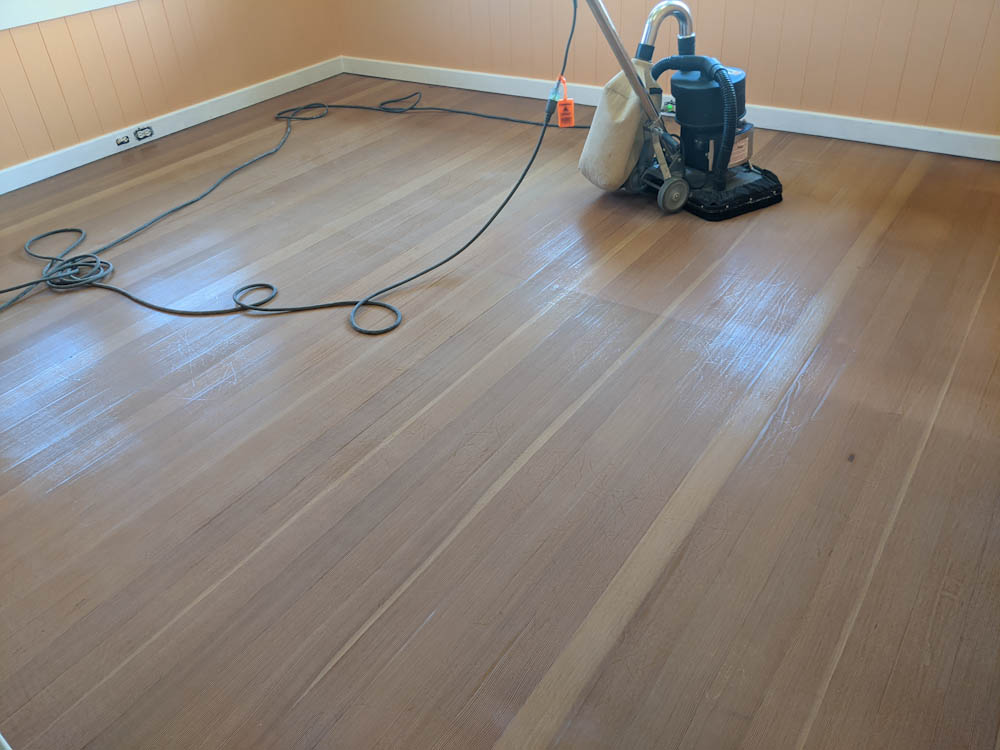
After going over the floor with the 220 grid screen the old finish has been matted down, except where the coat was a bit thinner and the sander hasn’t gotten to.
I’m pretty out of practice with the applicator, so the results were not exactly flawless, but the floor looks much better and will hopefully stand up for another decade now.
At this point, all that remains is to paint the baseboards which I left in primer to avoid damaging the paint when sanding the floor.