It’s now been almost 4 months since the last episode of the basement “un-finishing”. We didn’t finish with coating the floor in the room that flooded because I wanted to finish the drainage first. Since that’s now functional, it was time to finish that up.
After one more can of the EpoxyShield, the west room now looks like this:
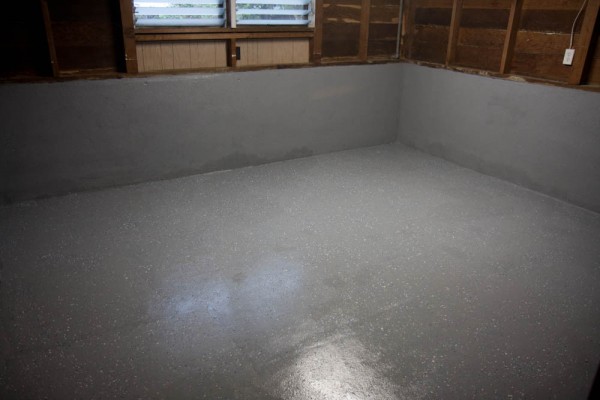
Finally the floor in the basement room is coated. We did the concrete walls too, just to make it look a bit cleaner.
Once that room had cured, we could now move all the stuff from the south room. To keep the boxes off the floor and get some air circulation around them, we got some shelving and this afternoon, the room looked like this:
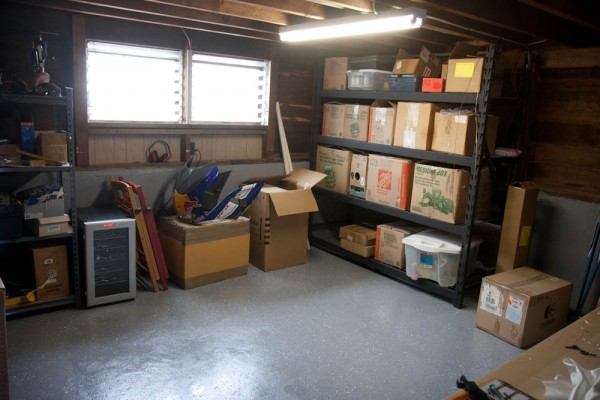
After moving all the stuff from the other room and the hallway, the west room is now full of stuff again.
That’s not all the stuff that was in the south room, a lot went into the north room where we now have a dehumidifier running. With all the rain we had a couple of weeks ago, we discovered a lot of stuff had gotten moldy. Things like backpacks and unused cutting boards, but also my motorcycle pants and leather belts. People say it’s basically impossible to not have stuff get moldy in Hilo, especially if you have it in storage. We figured it should be possible by sealing off one room and putting a dehumidifier in it, we could get the humidity down to “mainland values” without paying a fortune in the electric bill. In any case a lot of things that could get moldy is now stored in that room. We’ll see how it works out.
So that meant it was time to rip out the south room, which looked like this:
This room also has carpet, and it also got waterlogged when the basement flooded back around New Year’s. Time to rip that sucker out. After a bit of demolition work, it now looks like this:
The carpet here was actually laid on top of an old layer of linoleum, which is probably why it didn’t get quite as wet. Instead, the water must have seeped mostly under the carpet until it came out in the hallway on the other side of that room. One entire wall is concrete, because the front stairs are on the other side. This concrete was painted white, but the paint was bubbling due to efflorescence in several places, and there was a ton of “organic matter” between the concrete and the paneling. My guess would be decomposed cockroaches, judging from the few identifiable samples…
So now the room looks quite a bit more like a jail cell. But you gotta tear something down before you can build it up, right? Next is to get the floor grinder and take off the linoleum and clean up the concrete. The good part is that in the patches we could see, the floor looks in better shape than it did in the other room, so hopefully it’ll be a bit less work.