Progress has been a bit slow lately, but what I did get done since the holidays are some workshop improvements:
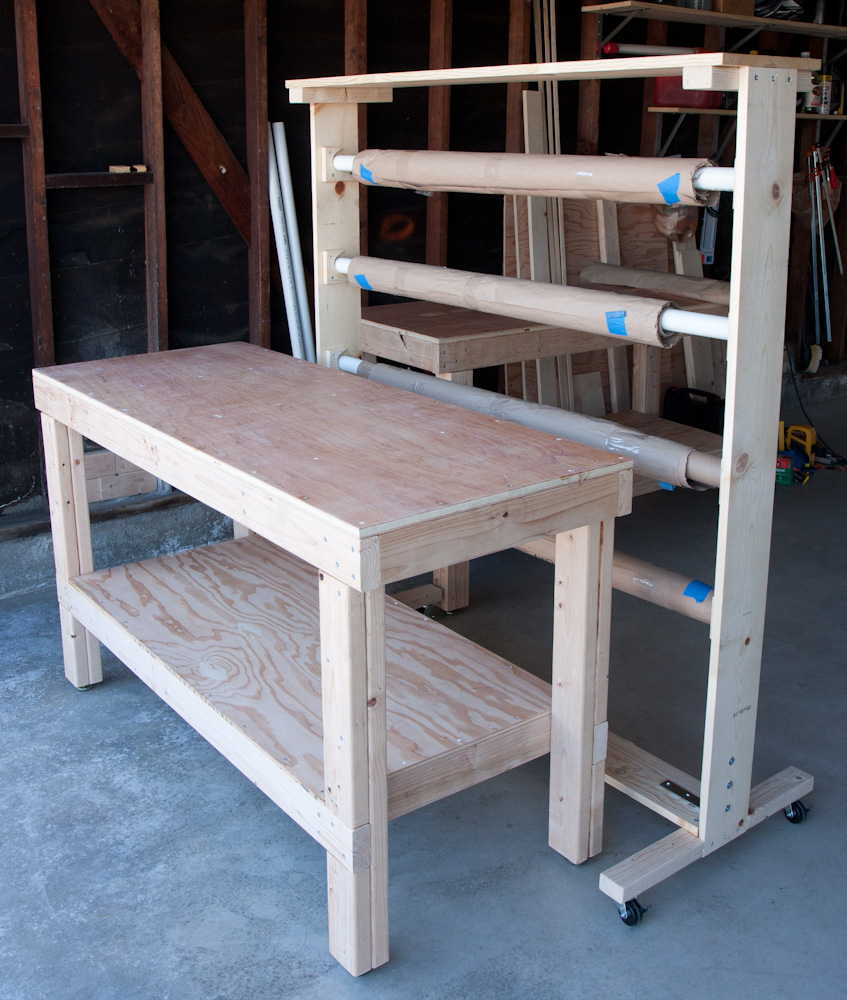
These are the two “EAA Chapter 1000” workbenches and the rack for fiberglass storage. The rack looks a bit empty with only my “preview rolls” on…
It’s been more of a “woodworking” than “composite construction” thing, but I now have 2 “EAA Chapter 1000” workbenches. These were designed by (you guessed it) EAA Chapter 1000, who realized that it was nice to have a standardized model of workbench that can be clamped together in various combinations if you need a larger one. They are 2x5ft, very sturdy, and have adjustable feet for leveling. The top is 3/4″ plywood that I “hard-shelled” with epoxy so that it’s very durable. Now I’ll have much more workspace for doing actual airplane layups.
Second was to arrange for some kind of fiberglass storage. The airplane requires about one full roll each of BID and UNI. Each roll is 125 yards and weighs something around 70 lbs. Some easy way of handling these and unrolling fabric for cutting needs to be arranged. A lot of people make a wall-mounted cabinet that can be closed for dust protection and where the door doubles as a cutting surface when open. I don’t have that kind of wall space, so that wouldn’t work that well for me. Instead, I came across the idea of building a movable cloth rack from looking at how other canard builders have set up their workshop.
The rack is a simple wooden setup that rolls on wheels and has room for 4 full cloth rolls. This way it can be rolled up to the table when cutting cloth, and then tucked away when not used. For dust protection, I’m going to hang sheets from the top surface so the cloth is covered when not in use.
With that done, it’s time to get back to some epoxy work.